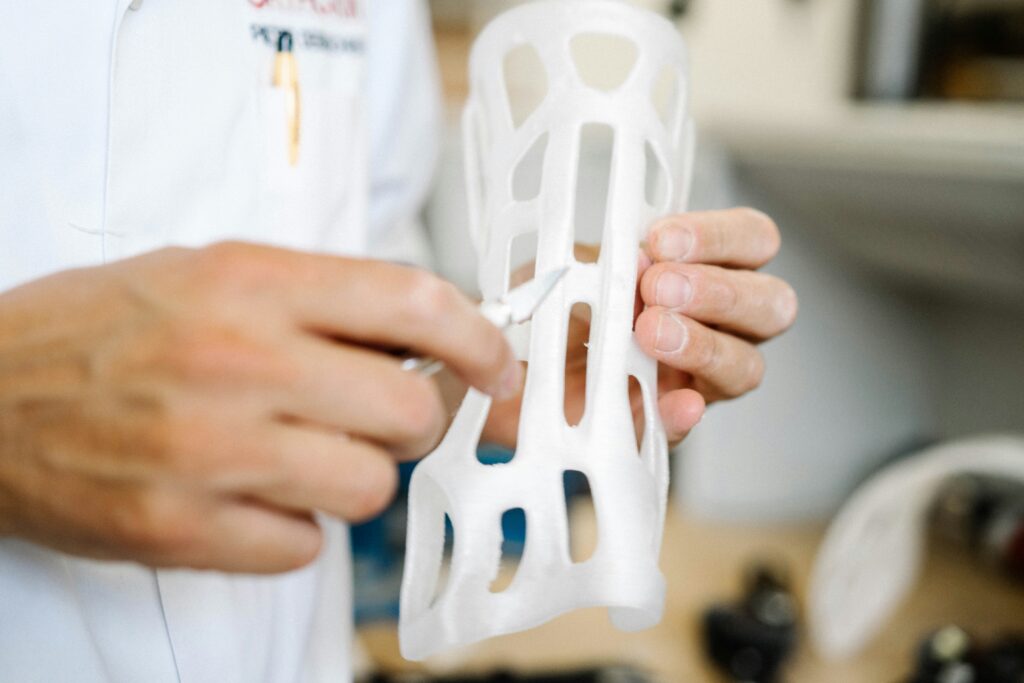
Affiliate Disclosure: This blog contains affiliate link. If you purchase through these links, I may earn a commission at no extra cost to you.
I. Introduction
Upper limb amputations affect individuals of all ages, with causes ranging from trauma and vascular diseases to congenital disorders. However, prosthetic accessibility remains severely limited. As we look toward shaping the future of prosthetic technology, it is crucial to address these barriers. The World Health Organization (WHO) estimates that nearly 40 million individuals require prosthetic limbs worldwide, yet only 5–15% have access to them.
Traditional prostheses are often expensive, ranging from USD 4000 to USD 75,000, making them unattainable for many, especially in underserved regions. Additionally, frequent replacements, particularly for pediatric patients, further increase costs and logistical challenges.
To address these barriers, 3D printing is shaping the future of prosthetic development. Unlike conventional manufacturing, which requires extensive tooling, additive manufacturing allows for cost-effective, customizable prostheses, significantly improving accessibility.
This blog examines how 3D-printed prostheses enhance affordability and personalization, exploring their methodologies, design evolution, and clinical applications.
II. Shaping the Future: Evolution of Upper Extremity Prostheses
Shaping the Future: Traditional Prosthetic Limitations
Historically, upper limb prostheses have been constrained by high costs, limited availability, and complex fitting requirements. Body-powered prostheses alone range from USD 4000 to USD 20,000, adding financial strain to individuals seeking functional limb replacements.
Moreover, acquiring prosthetic devices involves time-consuming appointments for measurements and fittings, posing additional barriers for patients.
Emergence of 3D Printing in Prosthetic Manufacturing
Three-dimensional printing builds prostheses layer by layer, eliminating traditional manufacturing inefficiencies. This approach enables low-cost, highly customizable designs, making prosthetic devices more accessible.
According to the review:
- 64% of 3D-printed prostheses cost under USD 50
- 14% cost between USD 50–100
- 22% cost over USD 100
These figures underscore the financial advantages of additive manufacturing over conventional prosthetic production methods.
The Role of Open-Source Platforms in Shaping the Future
Online repositories such as Enabling the Future, NIH 3D Print Exchange, and Thingiverse provide open-source prosthetic designs, allowing individuals and organizations to freely access, modify, and print prostheses.
The e-NABLE community, for example, plays a vital role in developing affordable, modular prosthetic models, particularly for children requiring frequent replacements.
III. Shaping the Future: How 3D Printing Enhances Prosthetic Development
Shaping the Future: Research Approach
This review followed a two-phase methodology to analyze the development and accessibility of 3D-printed upper limb prostheses. The first phase involved a literature search using relevant keywords, while the second phase collected prosthetic data from open-source platforms.
Data Sources
To ensure a comprehensive evaluation, three major online repositories were analyzed:
- Enabling the Future – The largest platform offering free 3D-printed prosthetic designs.
- NIH 3D Print Exchange – A biomedical repository featuring bioscientific and prosthetic models.
- Thingiverse – A community-driven database hosting innovative prosthetic designs.
Literature searches were conducted across PubMed, Embase, and the Cochrane Library using MeSH terms such as “3D printing,” “upper limb prosthesis,” and “additive manufacturing.” Only full-text papers published within the past ten years were considered.
Selection Criteria
Studies were selected based on the following parameters:
- Prosthetic Design – Evaluating form, function, and assembly complexity.
- Material Composition – Identifying the use of PLA, TPU, PETG, and other key materials.
- Clinical Applicability – Determining suitability for different patient demographics.
- Cost & Accessibility – Classifying prostheses into cost brackets for affordability analysis.
Categorization of Prostheses
All identified prostheses were grouped based on type, cost, and accessibility. The final review included 35 models, categorized into finger, hand, arm, and upper-arm prostheses. The following table presents an overview:
Prosthesis Type | Number of Models | Primary Material | Cost Category |
---|---|---|---|
Finger Prostheses | 2 | TPU, Nylon | Low (<USD 50) |
Hand Prostheses | 19 | PLA, ABS | Low to Moderate (USD 20–100) |
Arm Prostheses | 12 | PETG, PLA | Moderate to High (USD 50–300) |
Upper-Arm Prostheses | 2 | PLA, TPU | High (>USD 100) |
IV. Shaping the Future: Working Mechanism – Functionality and Design Innovations
Shaping the Future: Types of Prostheses
The reviewed prostheses were grouped into four categories:
- Finger Prostheses – Single-digit devices designed to enhance grip functionality.
- Hand Prostheses – Full-hand designs with wrist-driven movement.
- Arm Prostheses – Devices extending to the elbow with more complex control mechanisms.
- Upper-Arm Prostheses – Large-scale designs reaching the shoulder for full-arm mobility.
Hand prostheses were the most common, comprising 54% of reviewed models.
Actuation Methods
Prosthetic control mechanisms were classified into body-powered and externally powered systems:
- Body-Powered Prostheses (71%) – Relying on mechanical energy generated by wrist, elbow, or shoulder movements.
- Electromyographic (EMG)-Controlled Systems – Translating muscle signals into precise movements for enhanced control.
- Micro-Motor Powered Actuation – Used in advanced robotic prostheses for finer manipulation.
The following chart showcases the distribution of actuation mechanisms:
Material and Manufacturing Specifications
Common materials included:
- Polylactic Acid (PLA) – Durable, cost-effective, and widely used.
- Thermoplastic Polyurethane (TPU) – Flexible and elastic for improved grip.
- Acrylonitrile Butadiene Styrene (ABS) – Lightweight yet sturdy, used in high-performance prostheses.
- Nylon & Photopolymer Resins – Used in specialized biomedical applications.
Printing costs varied significantly. The majority of 3D-printed prostheses cost less than USD 50, compared to traditional devices priced up to USD 75,000.
Customization & Open-Source Impact
The rise of open-source prosthetic designs has significantly expanded accessibility. Enabling the Future and NIH 3D Print Exchange allow individuals and communities to collaborate, modify, and distribute prosthetic designs freely, promoting widespread innovation.
The following table compares key models based on cost, weight, and printing complexity:
Prosthesis Model | Cost (USD) | Weight (g) | Assembly Difficulty | Material Used |
---|---|---|---|---|
Cyborg Beast | 184 | USD 20 | Easy | PLA |
e-NABLE Phoenix Hand | 148 | USD 30 | Easy | PETG |
X-Limb | 253 | USD 200 | Moderate | TPU |
Adjustowrap Gripper Arm | 429 | USD 600 | Difficult | PLA, Nylon |
V. Results: Performance, Cost, and Accessibility
Prosthesis Classification: Weight, Flexibility, Grip Strength, and Adaptability
The reviewed prosthetic models showcased a broad spectrum of functionalities, weight classifications, and adaptability levels. The analysis of 35 models revealed significant variations in design specifications, actuation mechanisms, and kinematic features.
Weight Distribution Across Prosthetic Types
Prosthetic models varied in weight due to different materials and actuation systems. The lightest prosthetic hand, designed by Cuellar et al., weighed only 92 g, while the heaviest arm prosthesis, detailed by Cutipa-Puma et al., reached 1000 g. The average weight for hand prostheses was 274 g, whereas arm prostheses had a mean weight of 797 g.
Prosthesis Type | Minimum Weight (g) | Maximum Weight (g) | Average Weight (g) |
---|---|---|---|
Hand Prostheses | 92 | 429 | 274 |
Arm Prostheses | 240 | 1000 | 797 |
These findings highlight the lightweight nature of 3D-printed prostheses, making them comfortable for daily use.
Grip Strength and Range of Motion
Grasp capabilities were evaluated in 29 models, revealing varying power and precision grasp functionalities:
- Power Grasp: 29 models supported cylindrical, spherical, and hook grasps.
- Precision Grasp: 27 models facilitated pinch, tripod, and lumbrical grasps.
- Grip Strength: Models ranged from 8.3 N to 23 N, with 13 models classified as strong, 12 as moderate, and 5 as weak.
The range of motion (ROM) analysis revealed:
- MCP flexion: 40°–90° across 34 models.
- PIP flexion: 45°–100°.
- Thumb rotation: 30°–120°.
These results demonstrate the functional efficiency of 3D-printed prostheses in mimicking natural hand movements.
Cost Analysis: Increasing Prosthetic Accessibility
One of the most striking advantages of 3D-printed prostheses is their affordability compared to traditional devices.
Cost Distribution of Reviewed Models
The majority (64%) of 3D-printed prostheses cost under USD 50, making them significantly more accessible:
Cost Category | Percentage of Models |
---|---|
Low (< USD 50) | 64% |
Moderate (USD 50–100) | 14% |
High (> USD 100) | 22% |
Compared to traditional prosthetic devices, which range between USD 4000–75,000, 3D printing has drastically reduced financial barriers, particularly benefiting children requiring frequent replacements.
Clinical Applications: Rehabilitation Benefits, Especially for Children
3D-printed prostheses have shown potential beyond limb replacement, extending into rehabilitation protocols.
A case study on pediatric rehabilitation demonstrated the benefits of 3D-printed hand prostheses:
- Strength Improvements: Enhanced wrist flexion, extension, and forearm pronation.
- Coordination Gains: Increased sensory integration and motor control.
- Customization Advantages: Adjustable designs tailored for growing children.
These findings indicate the multifaceted role of 3D printing in healthcare, not only providing limb replacements but also enhancing rehabilitation strategies.
Challenges & Future Directions: Standardization, Clinical Validation, and Technological Enhancements
Despite the advancements in 3D-printed prostheses, several challenges remain:
- Lack of Standardized Guidelines
- No universal design protocols exist, leading to variability in performance and print quality.
- Limited Clinical Validation
- Few clinical trials verify the long-term effectiveness of 3D-printed prostheses.
- Technological Enhancements Needed
- Advancements in biomechanical functionality are necessary to improve grip force and responsiveness.
- The integration of electromyographic (EMG) control systems could enhance fine motor skills.
Addressing these challenges will be crucial for mainstream adoption of 3D-printed prostheses.
VI. Conclusion: The Future of 3D-Printed Prostheses
The evolution of 3D printing in prosthetic design is driving unprecedented accessibility and affordability. While traditional prostheses remain expensive, the open-source prosthetic movement is expanding low-cost, highly customizable solutions.
Need for Standardized Design & Testing Protocols
The future of 3D-printed prosthetics depends on the establishment of standardized guidelines, ensuring:
- Consistent print quality across manufacturers.
- Rigorous clinical validation for long-term effectiveness.
- Integration with biomechanical advancements for better movement control.
Potential for Mass Adoption in Healthcare
To accelerate adoption, interdisciplinary efforts must focus on:
- Expanding open-source collaboration through platforms like e-NABLE.
- Developing high-performance actuation technologies.
- Bridging the gap between research, engineering, and healthcare.
By overcoming these barriers, 3D-printed prostheses will continue shaping the future, providing accessible, functional solutions for individuals in need worldwide.
References & Licensing Information
This blog is based on insights from the following academic source:
Reference: Dababneh, S.; Dababneh, N.; Xie, C.; Henchi, H.; Efanov, J.I. Shaping the Future of Upper Extremity Prostheses Through 3D Printing. Prosthesis 2025, 7, 39. https://doi.org/10.3390/prosthesis7020039
License: This content is adapted from an open-access article under the Creative Commons Attribution (CC BY) License. You are free to share, adapt, and build upon this work, provided proper attribution is given to the original authors.