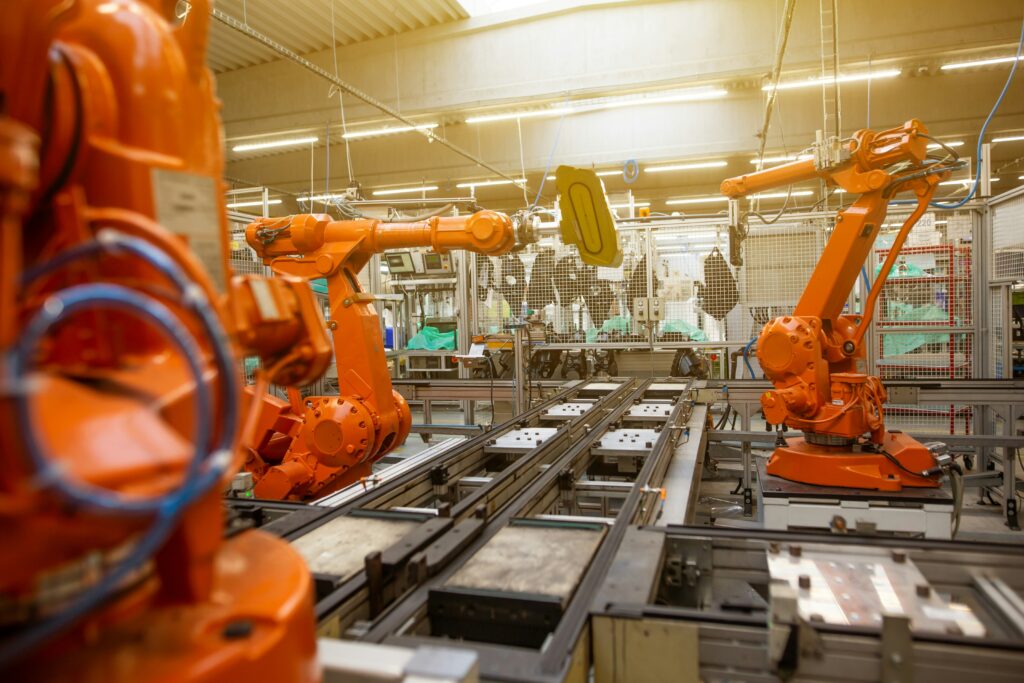
Introduction to Modular Control System
Industrial processes are advancing at an unprecedented pace, demanding solutions that are not only efficient and reliable but also scalable and adaptable. A key innovation addressing these demands is the modular control system. Companies like Beckhoff Automation, renowned for their industrial automation systems and modular hardware solutions, exemplify the potential of this approach. This cutting-edge technology combines modular architecture with edge computing principles to optimize performance, ensure reliability, and simplify system upgrades.
In this blog, we explore the intricacies of the modular control system—its architecture, methodology, benefits, and real-world applications. By seamlessly integrating local processing with modular hardware, this system represents a pivotal step toward smarter, more connected industries.
Architecture and Key Features of Modular Control Systems
The modular control system employs an architecture designed for industrial scalability and flexibility. It features two key components:
- Principal Module (mP): Functions as the system’s core, managing coordination and communication.
- Expansion Modules (mEXs): Designed for specific tasks, these modules capture and process field data locally.
The system’s modular architecture enables easy upgrades or replacements, fostering efficiency in dynamic industrial environments.
Key Features of the Modular Control System
Feature | Description |
---|---|
Plug-and-Play | Simplifies the addition and replacement of modules. |
EtherCAT Communication | Ensures real-time, deterministic data transmission. |
Local Processing | Reduces network latency and enhances efficiency. |
Electrical Protection | Includes EMC filters, galvanic isolation, and voltage regulation. |
Principal Module (mP)
The mP serves as the system’s control hub, enabling real-time communication between modules via EtherCAT. Key features include:
- Ethernet & EtherCAT Ports: For seamless communication and integration.
- Storage Capabilities: Incorporates SSD and SD card slots for data storage and system initialization.
- Hardware Protection: Ensures reliable operation under harsh industrial conditions.
Table: Principal Module Hardware Components
Component | Functionality |
---|---|
CPU (ARM Cortex A9) | Centralized control and processing. |
Ethernet & EtherCAT Ports | Facilitates high-speed data transmission. |
SSD & SD Card Storage | Provides robust data handling capabilities. |
Expansion Modules (mEXs)
The expansion modules (mEXs) are integral to the modular control system, capturing data directly from the field and processing it locally. Each mEX is equipped with:
- Signal Conditioning Circuits: Ensures compatibility with ADC input ranges.
- System-On-Chip (SoC): Houses a CPU and FPGA for flexible algorithm implementation.
- EtherCAT Slave Controller: Enables efficient communication with the mP.
Methodology and Workflow
Data Workflow in Expansion Modules
The modular control system’s local processing capabilities are implemented in the following steps:
- Data Acquisition: Sensors gather signals from the field.
- Signal Conditioning: Prepares signals for ADC conversion.
- Fourier Transform (FFT): Analyzes signals in the frequency domain.
- Curve Fitting (Cubic Spline): Reduces the data transmitted over the network.
Table: Data Processing Workflow
Step | Description |
---|---|
Data Acquisition | Captures signals from field sensors. |
Fourier Transform | Converts time-domain signals to the frequency domain. |
Curve Fitting | Compresses data while maintaining accuracy. |
Working of the Modular Control System
Principal Module Operation
The mP acts as the master controller, ensuring seamless interaction between modules. It stores critical data and enables centralized management through its advanced processing capabilities.
Expansion Module Operation
Each mEX specializes in specific tasks, such as:
- Electrical Signal Module (mSE): Analyzes three-phase power supply signals.
- Vibration Signal Module (mSV): Monitors and processes vibration data for applications like cement ball mills.
Case Study: Cement Ball Mill
Using the mSV module, vibration signals were analyzed to determine chamber filling levels in a cement ball mill. FFT and curve fitting were utilized to optimize grinding efficiency and reduce data transmission requirements.
Table: Cement Ball Mill Analysis
Chamber | Parameter Monitored | Result |
---|---|---|
First Chamber | Coarse grinding vibration levels | Accurate material level estimation. |
Second Chamber | Fine grinding vibration patterns | Reliable operational metrics. |
Results: Validation and Impact
Performance Metrics
- Data Efficiency: Reduced network dependency with post-processed data.
- Reliability: High accuracy in challenging industrial environments.
- Scalability: Modules can be easily added for new functions.
FFT and Curve Fitting
The combination of FFT and cubic spline algorithms enhanced network efficiency by transmitting only essential coefficients.
Discussion: Advantages of Modular Control Systems
Key Benefits
- Scalability: Add or replace modules with ease.
- Efficiency: Reduce network latency through local processing.
- Reliability: Operates effectively in harsh conditions.
Conclusion: The Future of Modular Control Systems
The modular control system is a game-changer in industrial automation, offering unparalleled scalability, efficiency, and adaptability. By leveraging local processing and edge computing, it meets the demands of modern industries with ease.
Summary of Benefits
- Enhances real-time data processing and efficiency.
- Simplifies system upgrades with Plug-and-Play functionality.
- Provides robust protection in demanding environments.
Future Directions
- Integrating advanced AI for predictive maintenance.
- Testing across varied industrial environments like biomass and wastewater plants.
- Transitioning to distributed architectures for greater reliability.
As industries evolve, the modular control system will play a critical role in shaping the future of automation, setting new benchmarks for performance, adaptability, and innovation.
References
- Gouveia, G.; Alves, J.; Sousa, P.; Araújo, R.; Mendes, J. Edge Computing-Based Modular Control System for Industrial Environments. Processes 2024, 12, 1165. https://doi.org/10.3390/pr12061165
- Mao, W.; Zhao, Z.; Chang, Z.; Min, G.; Gao, W. Energy-Efficient Industrial Internet of Things: Overview and Open Issues. IEEE Transactions on Industrial Informatics 2021, 17, 7225–7237.
- Teixeira, J.E.; Tavares-Lehmann, A.T.C. Industry 4.0 in the European Union: Policies and National Strategies. Technological Forecasting and Social Change 2022, 180, 121664.
- Alves, J.; Sousa, P.; Matos, B.; Mendes, J.; Souza, F.; Matias, T. Modular Cyber-Physical System for Smart Industry: A Case Study on Energy Load Disaggregation. In Proceedings of the 2023 International Conference on Control, Automation and Diagnosis (ICCAD), Rome, Italy, 10–12 May 2023; pp. 1–6.
(Include other references as appropriate based on your blog and paper content.)
CC BY 4.0 License Statement
This work is licensed under the Creative Commons Attribution 4.0 International License (CC BY 4.0). To view a copy of this license, visit https://creativecommons.org/licenses/by/4.0/.
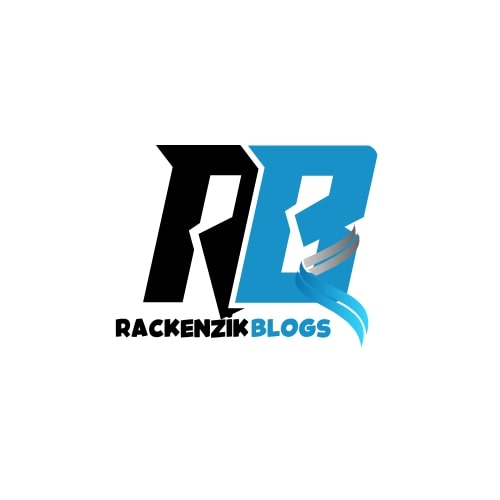