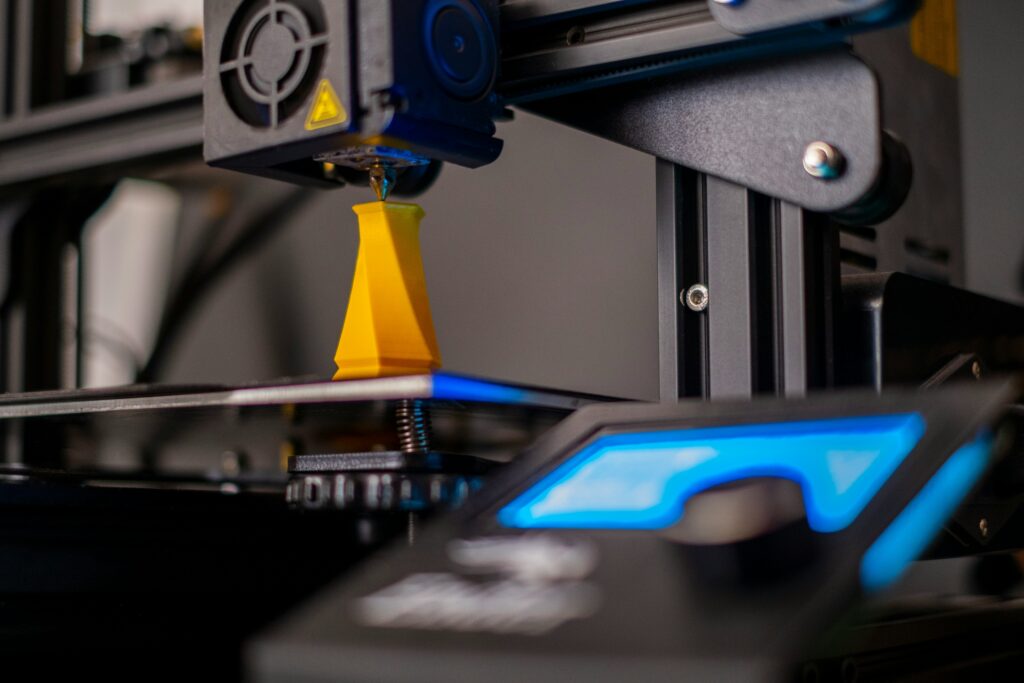
Introduction
Bending stress is a critical factor in achieving this optimization. It determines the resilience and structural integrity of AM components when subjected to perpendicular forces that cause bending. Addressing bending stress in additive manufacturing is key to ensuring that 3D-printed parts not only meet design specifications but also perform reliably under real-world conditions. By fine-tuning parameters like print orientation, infill pattern, nozzle temperature, and printing speed, significant improvements in mechanical properties can be achieved, as demonstrated through advanced methodologies such as FDM.
One of the most critical aspects of mechanical behavior is bending stress, which determines the ability of AM polymers, such as Polylactic Acid (PLA), to withstand applied loads without deforming or fracturing. Companies like Stratasys and EOS have been at the forefront of advancing additive manufacturing technologies, providing cutting-edge solutions to enhance the mechanical properties of 3D-printed components. This blog dives deep into experimental methodologies, analyses, and optimization techniques—offering valuable insights into the science behind bending stress in AM-produced components.
What is bending stress?
Bending stress occurs when a force is applied perpendicular to an object’s longitudinal axis, causing it to bend. It is a key parameter for evaluating mechanical performance in materials subjected to dynamic loads, making it particularly relevant for AM-produced components.
Relevance of Bending Stress in AM
Understanding bending stress in AM polymers helps manufacturers overcome challenges such as interlayer bonding weaknesses, anisotropic material behavior, and geometric irregularities. As AM parts are often used in structural applications, optimizing their ability to resist bending stress is crucial for achieving reliability and durability in real-world scenarios.
Bending Stress in Additive Manufacturing: A Key to Optimizing Mechanical Properties
What is AM?
Additive manufacturing, commonly referred to as 3D printing, is a process where material is deposited layer-by-layer to create objects directly from digital designs. This contrasts with traditional subtractive methods, which rely on carving materials from larger blocks.
Bending Stress in FDM Technology and PLA Material
One of the most widely adopted AM technologies is fused deposition modeling (FDM), a cost-effective approach to manufacturing objects with thermoplastic polymers. PLA (polylactic acid) is a popular choice due to its
- Biodegradability and eco-friendliness.
- Ease of printing and thermal stability.
- Mechanical properties suited for prototyping and structural applications.
However, PLA presents challenges under bending stress, particularly in the Z-axis orientation. Therefore, fine-tuning parameters like nozzle temperature, printing speed, infill pattern, and orientation is essential for optimizing performance.
Bending Stress in Methodology
Bending Stress in the Experimental Framework
This study employs Taguchi’s Design of Experiment (DOE) methodology, a statistical tool that simplifies complex experiments by systematically analyzing how manufacturing parameters influence mechanical properties. The experiments focus on maximizing two outputs:
- Maximum Load: The highest force the specimen can withstand before failure.
- Maximum Deflection: The distance a specimen bends before fracturing.
Selected Parameters
1. Nozzle Temperature (180°C–210°C)
Higher nozzle temperatures improve layer adhesion by promoting atomic diffusion but can introduce warping and cracking due to thermal expansion-contraction mismatches.
2. Printing Speed (25 mm/s–50 mm/s)
Slower speeds ensure consistent extrusion and bonding but compromise efficiency, while higher speeds reduce layer separation by minimizing cooling time between passes.
3. Infill Pattern
Three patterns were studied:
- Rectilinear: Balances strength and material efficiency.
- Honeycomb: Uses more material but reduces mechanical integrity.
- Triangle: Provides superior load-bearing properties.
4. Orientation (X, Y, Z)
Orientation determines how stress aligns with the layers of printed material, impacting strength and brittleness. X and Y orientations generally outperform Z due to improved interlayer bonding.
Three-Point Bending Test Setup
Specimens were manufactured under ASTM D790 specifications and subjected to bending stress using a Galdabini QUASAR 100 testing machine. The setup included an 8 mm square cross-section and a 60 mm active length between supports, with the load applied at a rate of 0.1 mm/s.
Results and Analysis
Experimental Findings
The tests yielded key insights into the mechanical behavior of AM specimens under bending stress:
Load and Deflection Data
Experiment | Temperature (°C) | Speed (mm/s) | Infill Pattern | Orientation | Max Load (N) | Max Deflection (mm) |
---|---|---|---|---|---|---|
1 | 180 | 25 | Rectilinear | X | 174.5 | 3.50 |
7 | 210 | 25 | Triangle | Y | 215.0 | 2.42 |
Impact Analysis
The study revealed that orientation had the most significant effect on maximum load (44.3%) and deflection (66.9%), followed by infill pattern, printing speed, and temperature.
Parameter | Impact on Load | Impact on Deflection |
---|---|---|
Orientation | 44.3% | 66.9% |
Infill Pattern | 28.4% | 13.1% |
Printing Speed | 16.6% | 14.4% |
Nozzle Temperature | 10.7% | 5.7% |
Predicted Optimal Settings
Combining optimal values for each parameter yields
- Load: 233.7 N with triangle infill, Y orientation, 210°C, and 50 mm/s speed.
- Deflection: 4.03 mm with rectilinear infill, X orientation, 195°C, and 50 mm/s speed.
In-Depth Conclusion
Key Insights
- Orientation’s Dominance: Specimens printed along the Y-axis outperformed others, with maximum loads increasing by 53.5%.
- Pattern Efficiency: Triangle patterns provided superior structural integrity, while honeycomb patterns consumed more material without proportional benefits.
- Temperature and Speed: Higher temperatures enhanced adhesion but showed diminishing returns, while faster speeds improved layer bonding.
Challenges and Future Directions
- Bed Adhesion Issues: Z-axis specimens often failed during printing due to poor adhesion.
- Standardization Needs: Inconsistent testing conditions across studies highlight the need for global benchmarks.
- Further Research: Investigating infill density-pattern efficiency and broader temperature ranges could yield additional insights.
Applications of Findings
Real-World Benefits
Healthcare: Improved prosthetics and orthotics capable of handling bending stress.
Aerospace: Enhanced bending resistance for lightweight aircraft interiors.
Automotive: Durable components for load-bearing applications.
References
Sagias, V.D., Papageorgiou, D.G., Pappas, A., & Stergiou, C.I. (2025). Mechanical Properties of AM Polymer Specimens Under Bending Stress. Applied Mechanics, 6(25). https://doi.org/10.3390/applmech6020025
CC BY 4.0 License
This blog is licensed under the Creative Commons Attribution 4.0 International (CC BY 4.0). You are free to:
- Share: Copy and redistribute the material in any medium or format.
- Adapt: Remix, transform, and build upon the material for any purpose, even commercially.
Under the following terms:
- Attribution: You must give appropriate credit, provide a link to the license, and indicate if changes were made. You may do so in any reasonable manner, but not in any way that suggests the licensor endorses you or your use.
For more information, visit: https://creativecommons.org/licenses/by/4.0/